Wedge Barriers for Beginners
Wiki Article
Some Of Wedge Barriers
Table of ContentsTop Guidelines Of Wedge BarriersThe Ultimate Guide To Wedge Barriers
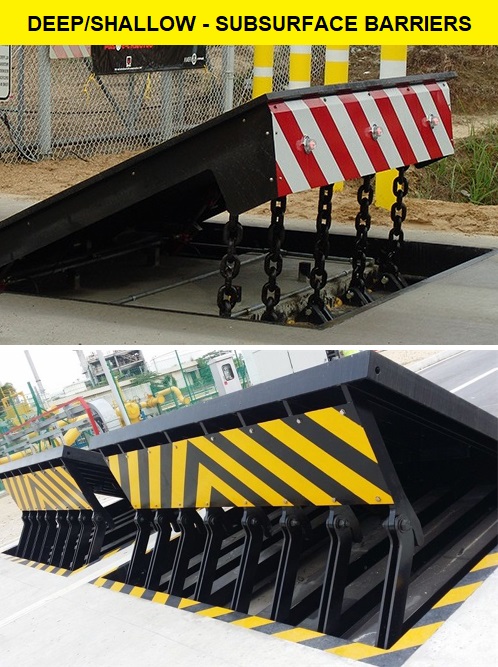
14 and the surface area 12 to which the obstacle 10 is safeguarded may be made from concrete - Wedge Barriers. 2, the barrier 10 is installed to or consists of an anchor or subframe (e. g., support 30 revealed in FIG. 2 )secured beneath the surface 12. For instance, the bather 10 might be bolted to the support or protected to the anchor by various other mechanical fasteners. In the illustrated personification, the obstacle 10 consists of a wedge plate 16, that includes a section that is significantly identical with the surface area 12 when the barrier 10 is in the retracted position. To put it simply, cars or individuals might pass over the barrier 10 when the obstacle 10 remains in the withdrawed setting and experience minor elevation loved one to the surface area 12 while on the barrier 10. As gone over thoroughly listed below, when the barrier 10 remains in the released setting, the wedge plate 16 is held and supported in an increased placement by a training device of the barrier 10. In addition, the parts 18 might be bolted or otherwise mechanically paired to each other. In this manner, fixing or replacement of several elements 18 may be simplified and structured. That is, fixing or replacement of solitary elements 18 might be done quicker, conveniently, and expense efficiently. FIG. In certain embodiments, the anchor 30 may be a steel frame including plates, beam of lights(e. g., I-beams ), and/or various other frameworks that are secured within the foundation 14, which may be concrete. At the surface area 12, a top side 28 of the anchor 30 may go to least partly exposed , therefore allowing the add-on of the obstacle 10 to the anchor 30. g., threaded holes)in one or even more light beams or plates of the support 30 may be subjected to the surface 12. In this fashion, bolts 32 or various other mechanical fasteners may be made use of to protect the barrier 10 to the anchor 30. As the barrier 10 is placed to the surface 12 of the structure 14, collection of particles and other product beneath the obstacle might be reduced, and components of the bather 10 might not be revealed to below grade atmospheres. As indicated by recommendation numeral 52, the training system 50 includes components got rid of beneath the wedge plate 16. The parts 52 under the wedge plate 16 might consist of an electromechanical actuator, a web cam, one or even more camera surfaces, and so forth. Furthermore, the lifting mechanism 50 includes a springtime setting up 54
The spring rod 58 is combined to a cam(e. g., webcam 80 received FIG. 4) of the lifting system 50. The springtimes 60 disposed about the springtime rod 58 are kept in compression by springtime sustains 62, consisting of a dealt with springtime assistance 64. That is, the fixed springtime support 64 is dealt with about the foundation 14 et cetera of the bather 10.
Wedge Barriers Fundamentals Explained
g., springtime support 65 )might be taken care of to the end of the spring rod 58 to enable compression of the springs 60. As the springs 60 are pressed between the springtime why not check here sustains 62, the spring setting up 54 produces a force acting upon the camera coupled to the spring rod 58 in a direction 66. As an example, the remaining force put on the webcam to deploy the wedge plate 16 may be supplied by an electromechanical actuator 84 or other actuator. The spring setting up 54 and the actuator 84(e. g., electromechanical actuator)might operate with each other to convert the camera and raise the wedge plate 16.
As mentioned above, the springtime setting up 54 exerts a consistent force on the camera, while the electromechanical actuator may be managed to apply a variable force on the web cam, thus enabling the training and reducing( i. e., deploying and retracting )of the wedge plate 16. In specific embodiments, the constant force used by the spring assembly 54 might be adjustable. g., electromechanical actuator) is disabled. As will be valued, the springtime setting up 54 may be covered and secured from debris or various other elements by a cover plate(e. g., cover plate 68 received FIG. 4) that might be substantially flush with the elevated surface 38 of the foundation 14. As discussed above, in the deployed setting, the wedge plate 16 offers to obstruct accessibility or travel past the obstacle 10. The barrier 10(e. g., the wedge plate 16 )might block pedestrians or cars from accessing a residential property or path. As talked about over, the obstacle 10 is connected to the anchor 30 protected within the foundation 14,
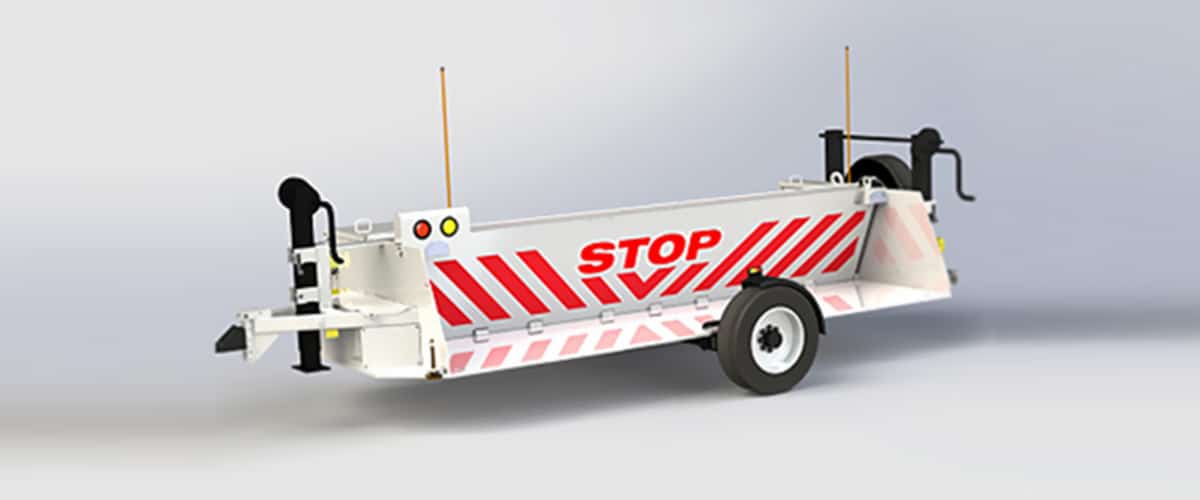
front braces 71. Therefore, the link settings up 72 might pivot and turn to make it possible for the collapse and expansion of the link assemblies 72 during retraction and deployment of the bather 10. The link settings up 72 reason movement of the wedge plate 16 to be restricted. If a vehicle is traveling in the direction of the deployed wedge plate 16(e. For example, in one scenario, the safety and security legs 86 may be expanded throughoutmaintenance of the barrier 10. When the security legs 86 are deployed, the safety and security legs 86 sustain the weight of the wedge plate 16 versus the surface 12. As a result, the lifting device 50 may be shut off, serviced, gotten rid of, replaced, etc. FIG. hop over to these guys 5 is partial perspective sight of an embodiment of the surface-mounted wedge-style barrier 10, illustrating the camera 80 and the camera surface areas 82 of the training mechanism 50. Specifically, two cam surfaces 82, which are described as reduced web cam surface areas 83, are positioned listed below the webcam 80. The reduced webcam surfaces 83 might be taken care of to the surface 12 (e. For example, the lower web cam surface areas 83 and the mounting plate 85 may create a solitary piece that is safeguarded to the anchor 30 by screws or other mechanical bolts. Furthermore, two cam surface areas 82, which are described as top camera surface areas 87, are positioned over the cam 80 and combined to (e. In various other embodiments, stepping check in layers or plates may be positioned in between the surface 12 and the reduced webcam surfaces 83 and/or the wedge plate 16 and the top cam surface areas 87 As mentioned above, the webcam 80 equates along the cam surfaces 82 when the wedge plate 16 is lifted from the withdrawed setting to the released setting. In addition, as stated above, the spring setting up 54 (see FIG. 3 )might provide a pressure acting upon the camera 80 in the instructions 102 through spring pole 58, which may minimize the force the electromechanical actuator 84 is called for to put on the camera 80 in order to activate and lift the wedge plate 16. 1 )to the released setting(see FIG. 4). As revealed, the web cam 80 consists of track wheels 104(e. g., rollers), which contact and equate along the web cam surface areas 82 throughout operation.
Report this wiki page